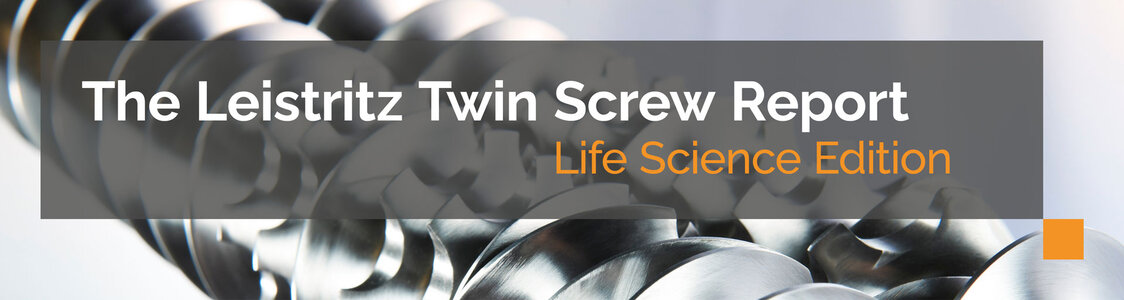
The following is included in this e-tech newsletter
- Featured article: Tips for successful air quench strand cooling for a melt extrusion process
- Troubleshooting formula: Peak Shear Rate & Shear Stress - Calculations that help manage mixing
- New technology: Effect of kneading disk geometry on twin screw melt granulation (TSMG)
- Technical article: Twin screw extruders as continuous mixers: A technical and historical perspective
- Leistritz Extrusion Technology expands process laboratory for implantable devices in the USA
- Life Science Twin Screw Workshop: Nov. 8-9, 2023 in Austin, TX
- Download the Leistritz Twin Screw Report Life Science e-newsletter as a pdf
Tips for successful air quench strand cooling for a melt extrusion process
Melting and mixing of polymers, APIs and excipients is performed by a twin screw extruder during the melt extrusion process. Volatiles (i.e. steam or residual solvents) are also removed during melt processing. The mixed/devolatilized melt is then pumped by discharge screw elements through a strand die that produces “spaghetti” strands, which must then be cooled, pulled and cut. Single or multiple strands are possible.
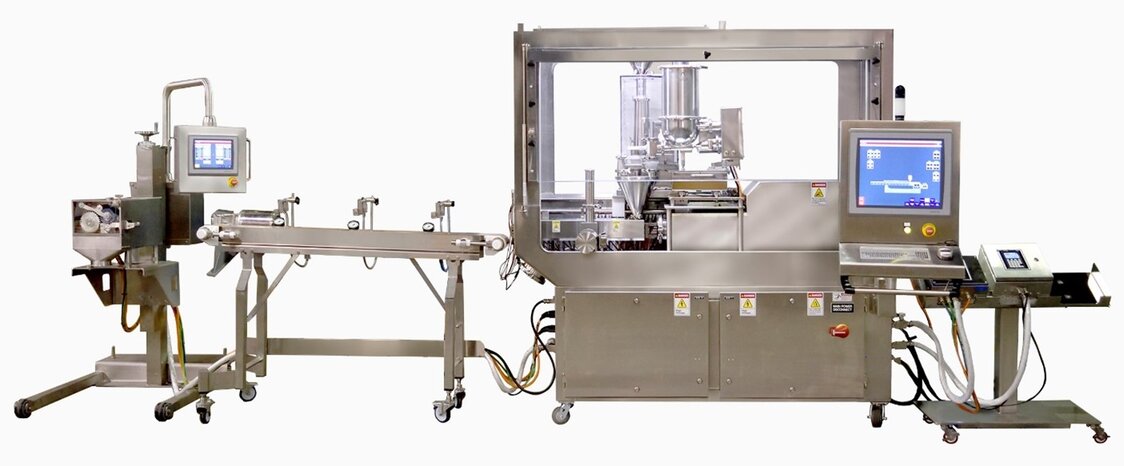
A ZSE 18 Air quench strand pelletizing system
To optimize dimensional tolerance, rheological characterization should be performed so that computer modeling can be implemented to optimize the flow path and die design.
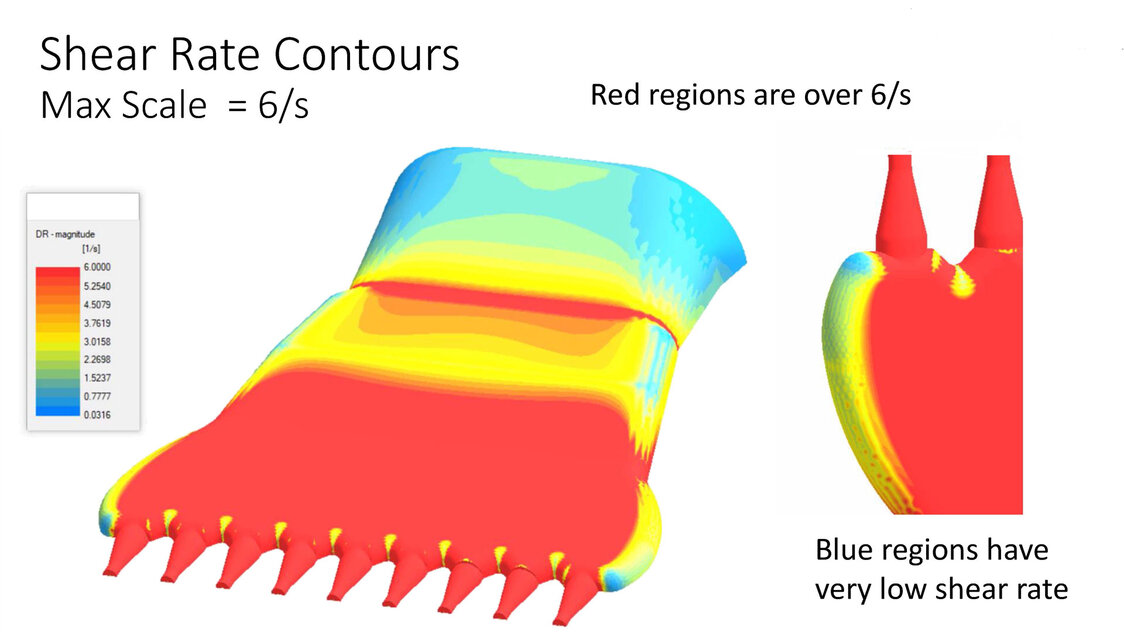
Example computer modelling for 9 strand die
The downstream process that cools and converts a melt extrudate into discrete and consistently sized pieces, called “pellets”, is referred to as pelletization. Pellets serve as the dosage itself, or as an intermediate part followed by a secondary milling operation.
The diameter of the pellet is determined by the die hole diameter, and the speed at which the strand is pulled away from the die. Hygienic design FDA compliant cooling belts that are equipped with auxiliary cooling devices are often specified to pull and support the strand(s) while cooling.
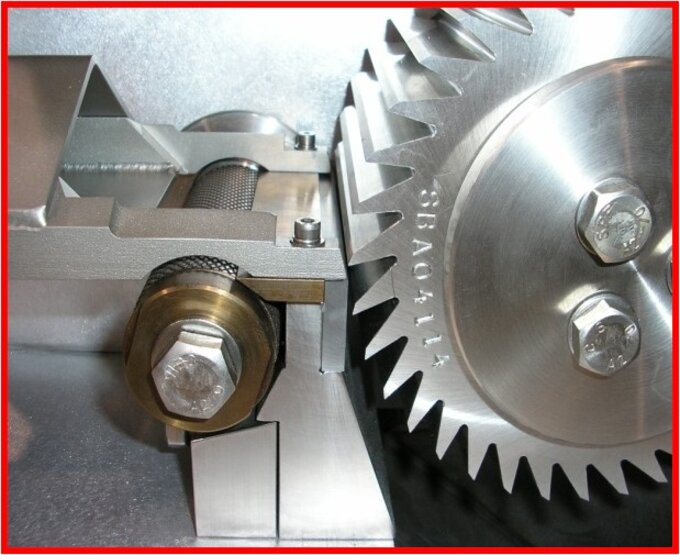
Multi-strand pelletizer cutting assembly
Traditional pelletizing systems utilize a rubber/knurled stainless steel pull roll assembly that pushes the strands to a bed knife/helical-cutter station. Pellet lengths, typically in the .8 to 6 mm range, are determined by the strand speed, cutter speed and number of cutting “teeth”. As many as 40+ strands can be pelletized, and a dual-drive pelletizer (1 for pull roll and 1 for cutter head) can be specified that allows different pellet lengths to be produced from the same unit.
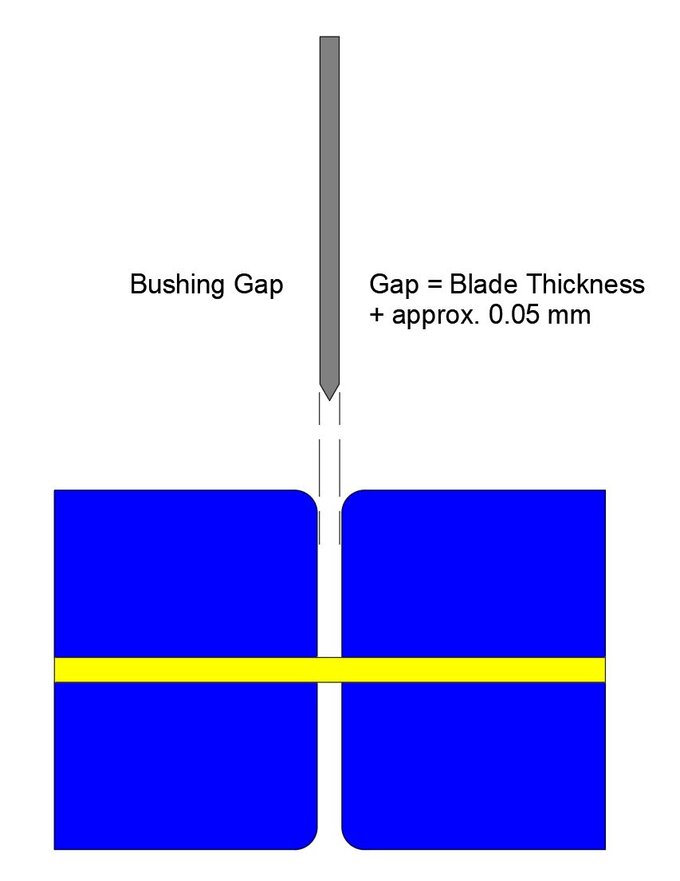
Bushing/cutter assembly for single strand parts
For a single strand, a 2-roll or belt puller can be substituted to push the strand into a bushing/knife assembly that slices strand. The bushing/knife assembly is customized for the diameter/length of the part, and the cutter can operate in on-demand and/or flywheel mode. Parts can be as short as ½ mm, with any length between ½ mm and 1 meter (or longer) being possible.
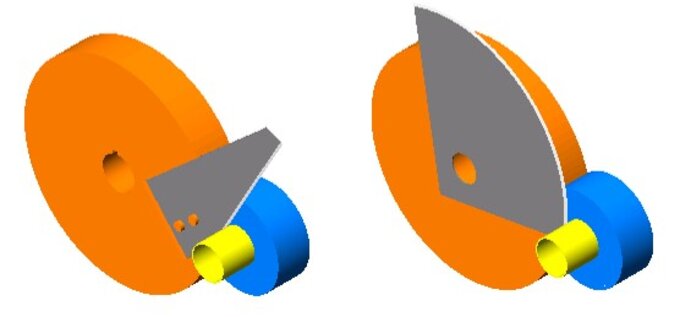
Bushing/cutter assembly for single strand parts
A non-contact laser scanner can be specified to measure, display and log the diameter of the strand(s). This device can also be integrated with the puller take-off speed for closed loop diameter control.
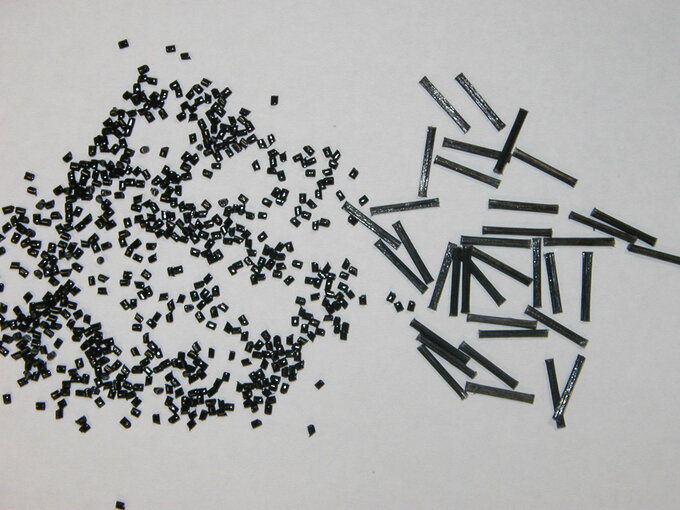
Example of 1 and 10 mm pellets/parts
Finally, after cutting, the pellets can be metered into a sieve device (called a classifier) to remove oversized and undersized pellets from the process.
Strand pelletizing systems are available for testing in the Leistritz USA process development laboratory.
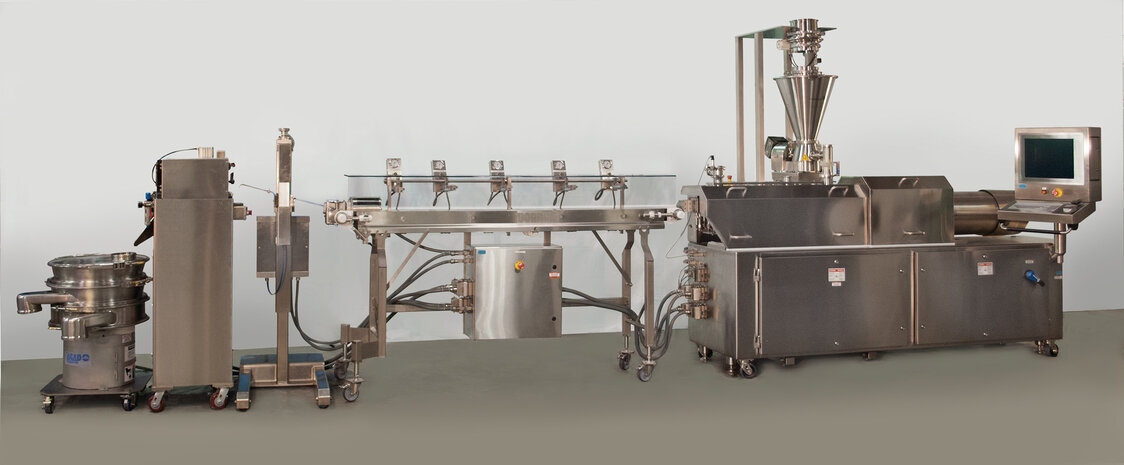
A ZSE 27 GMP strand pelletizing system with laser gauge and classifier
Peak Shear Rate & Shear Stress: How these calculations can help manage mixing in the melt extrusion process
Planar shear effects in the overflight gap of a kneading element, in combination with extensional mixing, are primary factors to facilitate mixing in a co-rotating, intermeshing twin screw extruder. Too much shear results in degradation, and too little yields not enough mixing. It’s a balancing act that’s challenging to quantify.
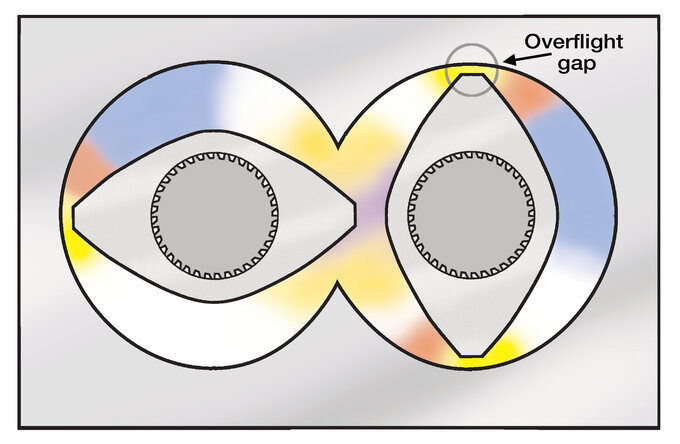
Although an imperfect solution, it can be helpful to benchmark the “peak shear” in the kneading/mixing screw zone(s), which is calculated using the overflight gap between the crest of the kneading element and the barrel wall.
Peak shear rate = (π*D*n)/(h*60) where:
D = screw diameter
n = screw rpm
h = overflight gap
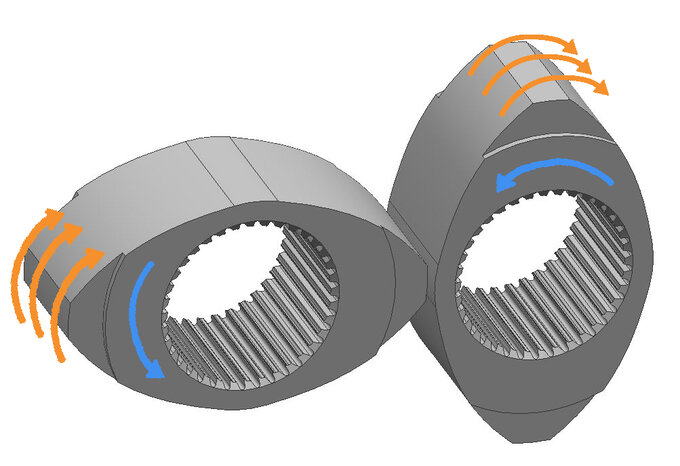
Example of overflight mixing effect in a co-rotating twin screw extruder
For example, a ZSE 27 model twin screw extruder with a 27 mm OD/diameter screw and 0.1 mm overflight gap operating at 400 screw rpms, the peak shear is calculated as follows:
Peak Shear Rate = (3.14*27*400) / (.1*60) =’s 5652 reciprocal seconds
Shear stress rate is what actually produces dispersive mixing, and is dictated by the viscosity of the melt as indicated by the Shear Stress calculation:
Shear stress = peak shear x viscosity
The higher the viscosity the higher the shear stress, and vice versa. In the early stages of the process section, high viscosities cause elevated shear stress forces. In the latter part of the process, viscosities decrease along with achievable shear stress effects. Barrels cooling can be used to increase the viscosity of the melt to improve dispersive mixing effects.
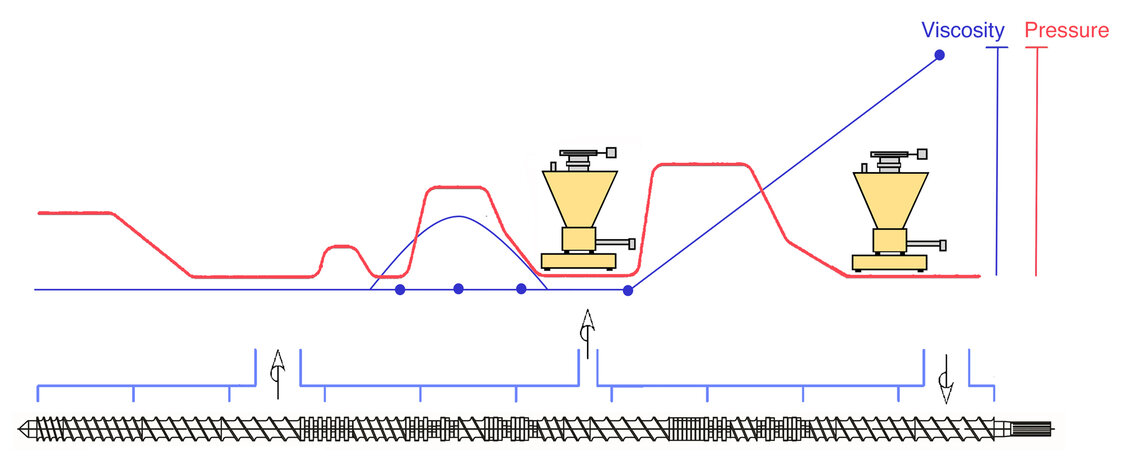
Example of pressure and viscosity profiles in a ZSE twin screw extruder
Extensional mixing is also an important parameter, resulting from accelerating and “stretching” mechanisms during the twin screw mixing process. (as compared to planar shear) Rheological characterization and computer modelling is required to quantify extensional mixing effects, which is why the simple Peak Shear Rate formula is often used as a quick and easy benchmark calculation.
A couple of ways shear stress can be managed is as follows:
- Pre-mixed materials can be metered into the main feed port to strategically target exposure to the high shear stresses rates in the early stages of the process to help achieve dispersive mixing (be aware of compaction effects that can occur that creates agglomerates)
- Shear sensitive materials can be introduced into a downstream zone via a side stuffer to avoid high shear stress inherent with melting to facilitate mix shear sensitive materials with minimal degradation
Effect of kneading disk geometry on twin-screw melt granulation
Twin-screw melt granulation (TSMG) relies on heat and mixing in the kneading zone(s) for granulation to occur. This study investigated the effects of novel kneading elements on drug stabilities by processing a mannitol (model compound) with hydroxypropyl cellulose as the thermal binder. Traditional kneading elements were engineered for plastics compounding and were then applied successfully to hot melt extrusion of amorphous solid dispersions.
The shear stresses inherent with traditional kneading/mixing elements seem excessive for melt granulation, in that in-process physicochemical changes such as drug degradation, polymorph changes, particle size reduction etc. have been observed.
Crystalline mannitol was the model compound for this study with hydroxypropyl cellulose (HPC) as the binder. Mannitol-HPC granules were processed on a Leistritz ZSE-18 twin-screw co-rotating, intermeshing twin screw extruder with a 25 L/D barrel configuration.
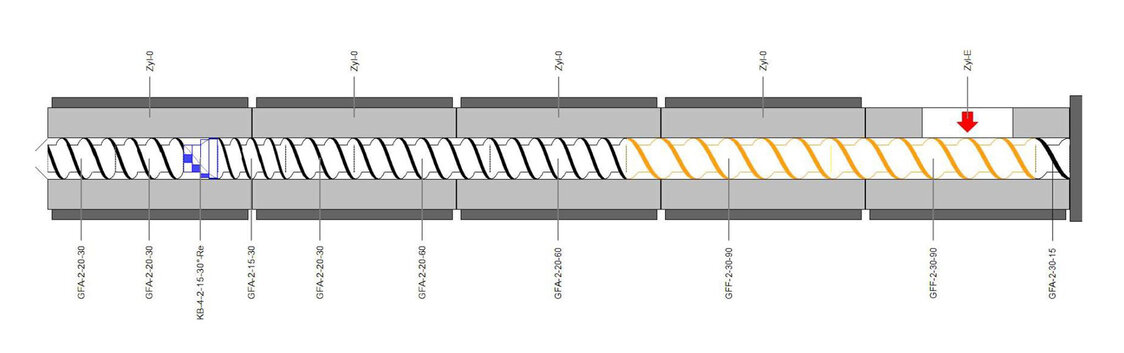
Granulation screw design
Reducing the kneading disc width and increasing the overflight clearance seemed to lower viscous dissipation. The reduced mixing, due to a lower peak shear, was compensated by increasing the staggering angle to achieve good granule tablet-ability. Increased staggering angles resulted in significantly stronger granules with a lower barrel temperature.
Twin screw extruders as continuous mixers: A technical and historical perspective
Developed approximately 100 years ago for natural rubber/plastics applications, processes via twin screw extrusion (TSE) now generate some of the most cutting-edge drug delivery systems that are available. The well characterized nature of the TSE process lends itself to ease of scale-up and process optimization while also affording the benefits of continuous manufacturing. Interestingly, the evolution of twin screw extrusion for pharmaceutical products has followed a similar path as previously trodden by plastics processing pioneers.
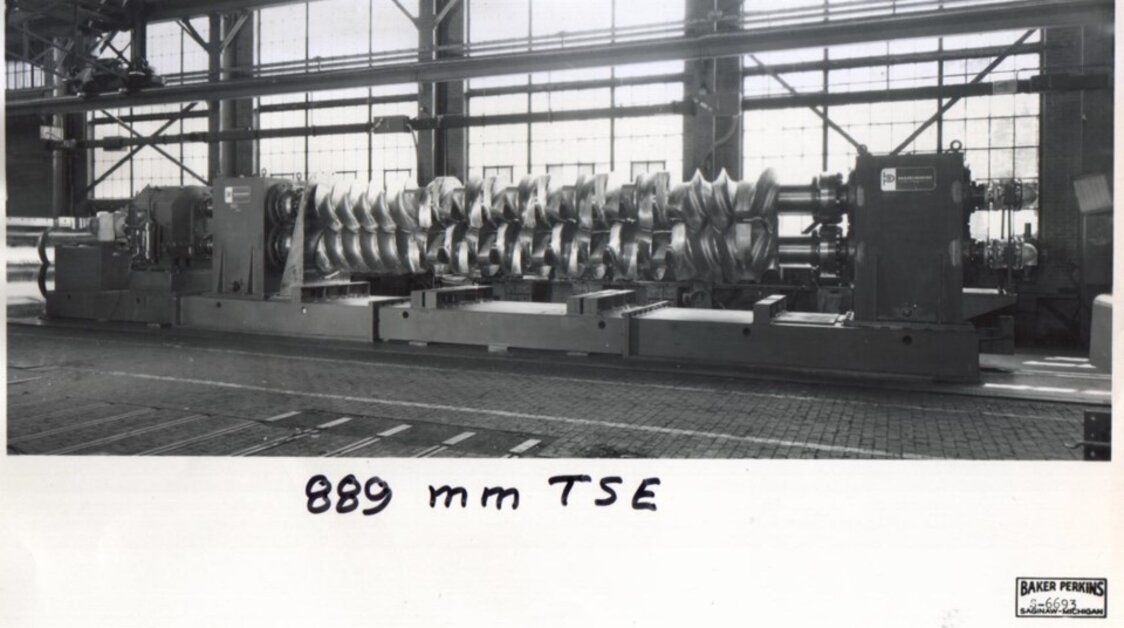
Old time 900 mm twin screw extruder from the 1960s used by the US Government
Almost every plastic has been processed at some stage in the manufacturing train on a twin screw extruder, which is utilized to mix materials together to impart desired properties into a final part. The evolution of processing via TSEs since the early/mid 1900s is recounted for plastics and also for pharmaceuticals from the late 1980s until today.
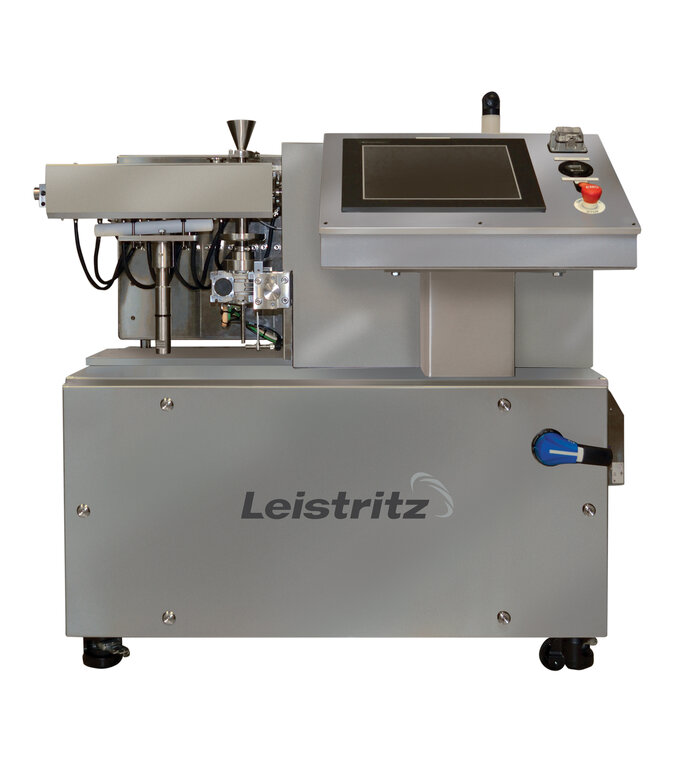
The similarities between plastics and pharmaceutical applications are striking. Today, twin screw extrusion is a battle hardened, well-proven, manufacturing process that has been validated in 24-h/day industrial settings. The same thing has happened with the extrusion technologies that are being applied today to advanced Life Science twin screw systems.
Leistritz Extrusion Technology expands process laboratory co-extrusion technologies for implantables in the USA
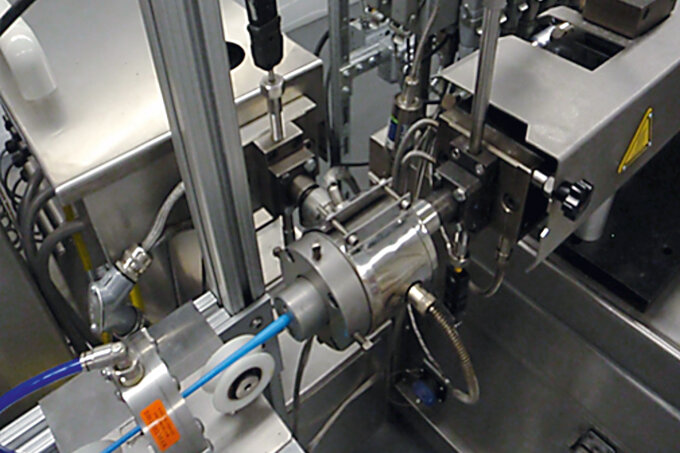
Co-extruded rod/ tube being developed in the Leistritz Process Lab
The Leistritz Extrusion USA Process Laboratory has recently added co-extrusion capabilities to allow users to develop products with two or more layers for subdermal and ocular implants. It is also possible to coat filaments or rods, similar to a coated wire.
Historically implants were simple mono-compositional rods designed to provide sustained drug delivery with a limited active lifetime. The desire to extend the treatment cycle to four+ weeks has motivated drug companies to develop multiple layer implants with unique geometries.
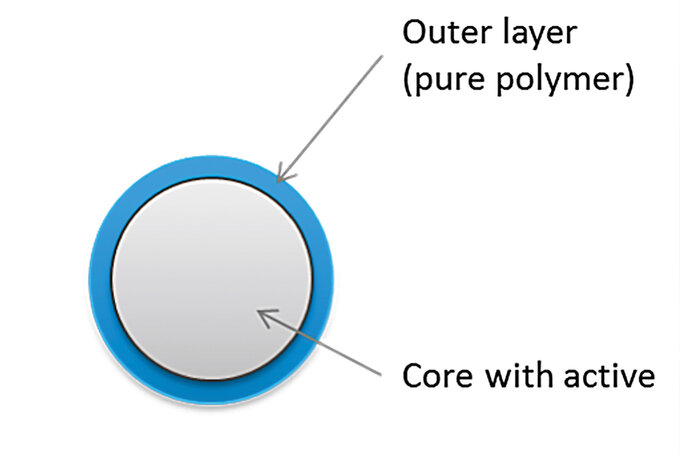
Co-extrusion systems are available to process a wide range of synthetic and natural biodegradable materials including PLA, PLGA, PGA, PEO, MC, HPC, HPMCAS and lipids; as well as bio-durable materials like silicone and EVA. Samples can be produced with as little as 500 grams of material.
A full assortment of feeders for handling pastes, slurries and powders are on-site, as well as downstream equipment for handling the wide-ranging implant devices. Parts can be wound or cut-to-length.
In addition to rods and tubes, a wide variety of coex film, sheet and laminates can be tested and developed in this facility.
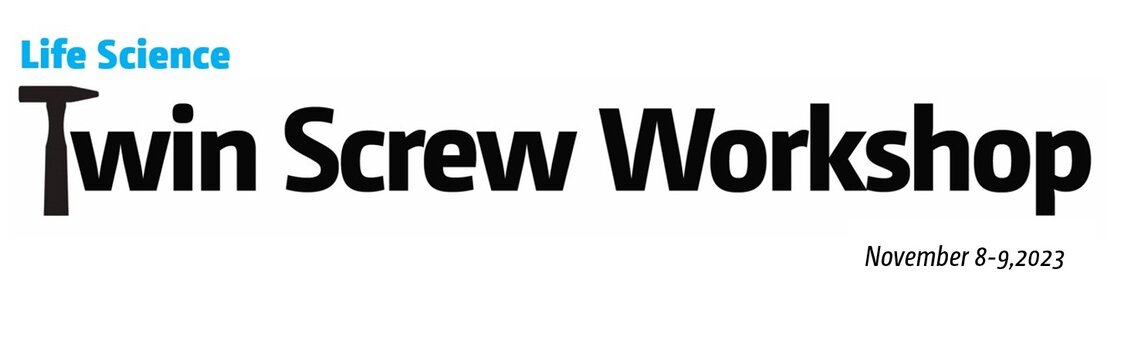
It’s a workshop, not a conference!A warm invitation – come and join our upcomoing Leistritz LifeScience Twin Screw Workshop!
November 8-9, 2023
Classroom sessions:
HOLIDAY INN EXPRESS ARBORETUM AREA, Austin, TX
Hands-on sessions:
The University of Texas at Austin - College of Pharmacy
The Leistritz Life Science Extrusion Workshop is unique in that classroom sessions are supplemented by interactive "hands-on" extrusion demonstrations.
The program agenda is as follows
Day 1
Wed., Nov. 8, 2023
Holiday Inn Express, Austin TX
Co-rotating and counterrotating twin screw
extrusion technology
- Screw design
- Theory, tips and test results
Continuous extrusion theory, tips and test results
- Melt extrusion
- Melt granulation
- Wet granulation
Feeders and material handling for pellets, powders and liquids
Downstream systems
In addition to Leistritz, outside speakers from industry and academia will contribute.
Day 2
Thurs., Nov. 9, 2023
University of TX/Austin laboratories
"Hands-on" demonstrations at the UT process development laboratory
- Twin screw extrusion systems in operation
- Assembly, and disassembly of twin screw elements
- Cleaning and maintenance of twin screw extruders
1:30 pm Lunch/adjournment
Cost: $800 prior to October 15th; $880 thereafter (includes handouts, lunches, and dinner on day 1)
More details/ register for the Leistritz Extrusion Life Science Extrusion Workshop
We look forward to serving you in the future.
For additional information on anything contained in this newsletter please contact us
Team @ Leistritz Extrusion
Leistritz Extrusion Technology
175 Meister Ave. Somerville, NJ, 08876, USA
Tel: 908/685-2333
Email: sales@leistritz-extrusion.com
Website: extruders.leistritz.com